Vacuum Casting Services in the UK
- Rapid quoting within 48 hours
- Durable parts with production-level quality
- Low-cost and quick turnaround for high-quality plastic parts
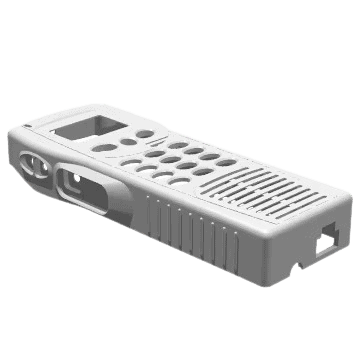
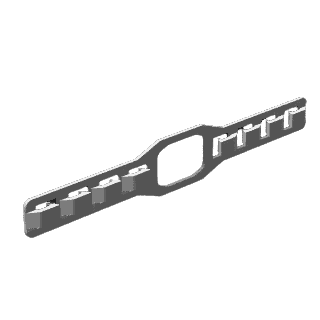
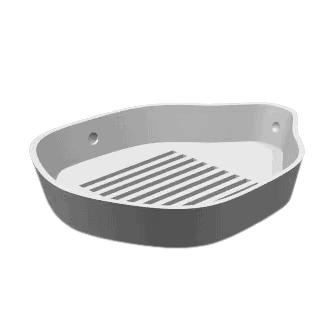
Start A New Casting Quote
STEP | STP | SLDPRT | STL | IPT | 3DXML | CATPART | PTC | PRT | SAT | PDF
Vacuum Casting Process
Vacuum casting is a technique for producing end-use, rigid, flexible, and rubber parts with production-level quality. This process uses a 3D printed master pattern and silicone moulds to produce high-quality, short-run parts up to 2300 mm long. The finished dimensions of urethane cast parts depend on the accuracy of the master model, part geometry, and casting material.
Vacuum cast parts are frequently used when colour, surface quality, and toughness are required. Vacuum casting is a perfect alternative for insert moulding in low volumes and is compatible with a wide range of materials. Polyurethane casting can also be used for bridge tooling between a 3D printed rapid prototype and injection moulding to effectively balance quality, cost, and time. Vacuum cast parts can also be clear, colour-matched, painted, have installed inserts, and even custom finished.
Applications of Vacuum Casting
Low-volume production
Vacuum cast parts are perfect for low-quantity production—when volumes don’t justify investment in injection mould tooling—and for first-run production parts, which can be completed weeks before production tooling is ready.
Advanced prototyping
The vacuum casting process and relatively inexpensive tooling involved make it easy and economical to make any necessary design changes. Additionally, different materials can be used with the same mould, which lets you test designs with a variety of materials.
Market testing
End-user functionality and high-quality finishes make vacuum cast parts ideal for consumer testing, user evaluation, and concept models. Using the cast urethane process means that changes can be incorporated quickly for either further testing or market launch.
Vacuum Casting Materials Selection
- ABS (PU8150)
- ABS (PU8260)
- ABS (PU8263)
- ABS (PX100)
- ABS (PX1180)
- ABS (PX215)
- ABS (UP4280)
- PC (PU8098)
- PC (PX510)
- PC (UP6160)
- PC-ABS (PX223HT)
- PMMA / Acrylic (PX5210HT)
- PMMA / Acrylic (UPX5210)
- PMMA / Acrylic (X522HT)
- PP (8550)
- PP (PU8570)
- PP (UP5690)
- Rubber (PU8400)
- Rubber (T0387)
Why Xometry UK Is the Right Partner for Your Vacuum Casting Projects
Lead times
Depending on the part design complexity, and the required quality of part surfaces, prototyping with vacuum casting can take 15-25 days.
Manufacturing volume
Vacuum casting is best suited to low-volume prototyping up to 20 units which you can get from one mould. You can increase the number of required units, but it will impact your project cost as additional moulds will be required.
Material selection
Choose from more than 15 plastic materials for casting projects.
Skilled engineering team
Our experienced team of casting engineers will guide you through every step of the process.
Vacuum Casting Tolerances
Tolerance values in vacuum casting depend on part dimensions and design complexity. The table below provides example tolerances based on various dimension ranges*:
Dimensions (mm) | 0 — 25 | 25 — 50 | 50 — 75 | 75 — 100 | 100 — 125 | 125 — 150 |
Tolerance (mm) | ±0.3 | ±0.35 | ±0.4 | ±0.45 | ±0.5 | ±0.55 |
*The values provided are illustrative. Tolerances should be determined individually for each vacuum casting project based on 2D drawings and CAD models of the specific part. For parts larger than 150 mm, please supply a 2D drawing and discuss tolerance requirements with your account manager.
Description | Tolerance Notes |
Distance Dimensions | Irregular or overly-thick geometries may cause deviances or deflection due to shrinkage |
Surface Quality | Surface finish is externally smoothed to a satin or matte surface. Grow lines may be present on internal or difficult-to-access features. Polishing or custom finishes must be clearly defined and agreed upon at the point of order |
Feature Definition | Sharp corners and text may appear slightly rounded |
Size Recommendation | We can offer vacuum cast parts as large as 2,000 mm long |
Vacuum Casting Fundamentals
Vacuum casting is a manufacturing process that provides end-use, rigid, flexible, and rubber parts with production-level quality. The vacuum casting process uses a Polyjet or SLA 3D-printed master pattern to create a silicone mould that produces high-quality, short-run parts as an cost-effective alternative to low-volume injection moulding.
Vacuum casting is similar to injection moulding in that it requires a tool with a cavity in the shape of the final part. The major difference is that vacuum casting uses a “soft” mould made of silicone whereas injection moulding uses a “hard” metal mould that has been CNC machined.
This soft mould wears out more quickly, which is the main drawback of vacuum casting. However, the process is significantly cheaper for low-volume and prototype plastic parts that require production-level quality and surface finishes.
The vacuum casting process has 3 major steps:
- The Master Pattern: Step one involves creating a master pattern of the final part using an additive manufacturing process. The most commonly used printing processes are Polyjet 3D or stereolithography (SLA) 3D due to their ability to produce parts with high resolutions and naturally smooth finishes. The master pattern is typically hand-finished to achieve optimal surface detail before the mould tool is created.
- Moulding: In step two, the 3D printed master pattern is encased in liquid silicone that cures around the pattern, with the silicone encapsulating all the features of the printed parts. When the mould cures, it is cut into distinct halves and the master pattern or 3D printed part is removed. This leaves an internal cavity exactly shaped like the part.
- Pouring: In the final step of the vacuum casting process, silicone is poured into the silicone mould, and the mould is then placed in a chamber to help remove air bubbles in the liquid material. For opaque parts, the chamber is typically pressurised. For clear parts, the chamber typically pulls a vacuum to mitigate any bubbles and increase clarity. Once cured, the silicone halves are separated and the newly formed part is removed. This process is repeated until the desired quantity is achieved.
One of the key distinctions between vacuum casting and 3D printing is material performance and quality. Vacuum casting offers higher-performing materials that can better emulate those used in commercial products. In addition, the fit and finish are often better with vacuum cast parts. If material performance and appearance are important to you, you should seriously consider vacuum casting.
The deciding factor between vacuum casting and injection moulding is quantity. Vacuum casting is an excellent option for very low quantities (e.g., 50 pieces) of production-grade parts. Compared with vacuum casting, injection moulding will have higher upfront tooling costs that may not be justified by a low-quantity run. Our customers often use vacuum casting as a stepping stone to test and refine their design before they invest in an injection moulding tool.
Xometry Also Offers These Services
Xometry: Experts in Sourcing Vacuum Cast Parts
All uploads are secure and confidential.